2D Code Marking
The demand for smaller and thinner products continues to grow across multiple industries, and these products often require detailed traceability. As a result, there's a need to pack more information within limited space.
Fortunately, 2D codes can hold tens to hundreds of times the information that a barcode can. This high information density allows a 2D code to hold the same amount of information in as little as 1/30th the size. These advantageous characteristics have led to expanding applications in various fields.
2D code application examples
Using 2D codes simplifies management, improves accuracy and reduces labor hours. In recent years, detailed traceability has been demanded for finished parts and their individual components. The number of 2D codes directly marked with a laser marker is increasing. Consequently, high quality marking is required to ensure stable 2D code reading is possible.
Electronic Device Industry

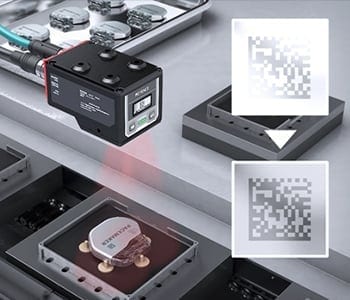
Automotive Industry
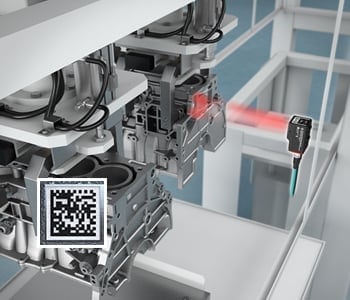
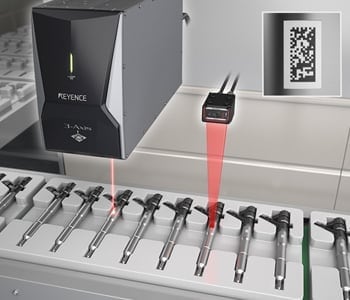
2D code grading
是很重要的创建很容易再保险的标志ad by 2D code readers in order to ensure stable reading. There are some standards for 2D code reading that can be used as a marking guide. Ease of reading can be expressed in grades. A standard called ISO/IEC TR 29158 (AIM DPM-1-2006)* is generally used to judge direct marking on products with laser markers. This standard specifies the following criteria for the evaluation of reading grades.
This is an international standard for 2D code marking quality evaluation of direct part marking.
- 1 Total judgment (All)
-
The total judgment is determined as the lowest grade among criteria 2 to 11. The result is expressed as a letter grade from A to D or F, where A is the highest grade (reading stability).
- 2 Decoding success/failure (DEC)
- Evaluation of whether decoding (reading) is possible or not
- 3 Cell contrast (CC)
- Difference in the average light intensity values between bright cells and dark cells
- 4 Cell modulation (CM)
- Evaluation of the variation in the brightness of bright cells and dark cells
- 5 Reflectance margin (RM)
- Evaluation by adding the judgment accuracy of bright and dark cells to CM (4).
- 6 Fixed pattern damage (FPD)
-
Degree of damage to the fixed pattern (see the figure below)
- 7 Format information damage (FID)
-
Degree of damage to the format information of a QR code (see the figure below)
- 8 Version information damage (VID)
-
Degree of damage to the version information of a QR code (Model 2 version 7 and later)
- 9 Axial nonuniformity (AN)
-
Degree of distortion of the vertical and horizontal sizes of a code
- 10 Grid nonuniformity (GN)
-
Evaluation of the largest misalignment among cell positions
- 11 Unused error correction (UEC)
- Ratio of error corrections that are not used for decoding
When directly marking metal surfaces, CC, CM, RM and FTP are often lower when contrast can't be obtained. Keeping these values high is the goal to ensure readable marking. Recently, C grades have become an industry standard and many companies are trying to grade codes immediately after marking them.
High-contrast marking
Accurately reading/grading 2D codes requires high contrast between black and white cells. Laser markers can produce black and white marks on metal depending on the marking parameters.
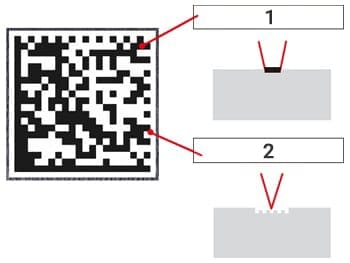
- 1. Black annealed marking
- Lasers create black marks on metal by oxidizing (burning it) or annealing it (using heat to create a black film).
- 2. White etching marking
- Lasers create white marks on metal by etching away the surface. This causes irregular light reflections, which makes the marking appear white.
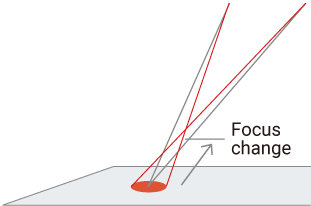
Contrast is important for 2D code marking. 3D correction is an effective method to maintain focus over the entire area.
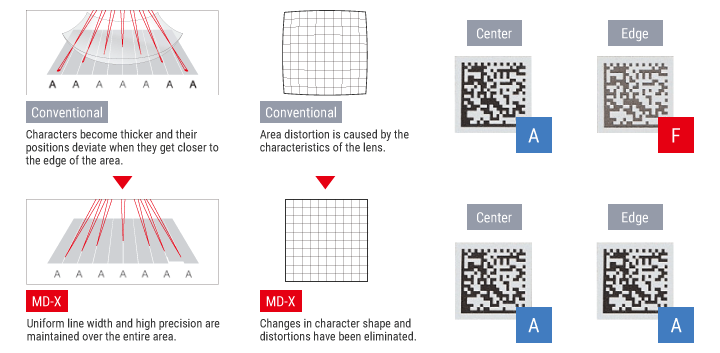
Ideal marking is possible at the center of most marking areas without any problems. However, lasers that don't have 3-Axis marking may find it difficult to create a clear contrast between black and white towards the outer edges of the marking field, resulting in lower grades.
Depth of focus
A laser beam has a depth of focus. When the focus deviates, the quality of marking degrades and this also affects 2D code reading.
2D code grade changes in accordance with focal distances
As a target moves further away from a laser's focal point, it becomes nearly impossible for the laser to create any contrast. Although a laser's depth-of-focus varies depending on the oscillation method, it is necessary to prevent the focus from deviating too much. This can be accomplished by an external displacement sensor or a built-in autofocus.

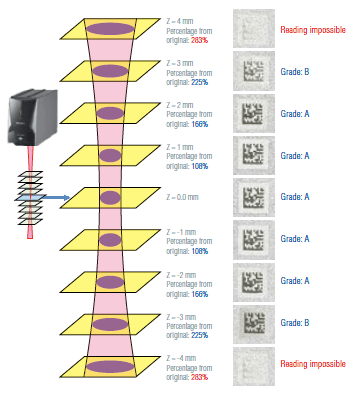
Laser oscillation method and depth of focus
The figure on the right compares the marking quality between a YVO4laser and a fiber laser. A YVO4laser produces a beam with a high peak power and a short pulse. This allows the laser to irradiate parts with ideal strength and high energy density over short time. Even when the focus deviates (due to movement of targets or product tolerance), a YVO4laser's marking quality is stable compared to fiber types. For cases where the marking is affected by an incident angle (such as at the edge of a marking area), a YVO4laser achieves stable marking quality without fading.
Keyence's MD-X Series combines the power of fiber and the quality of YVO4together via a unique oscillation method.
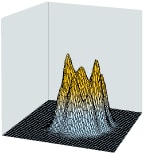
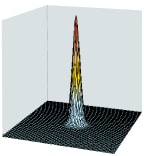
(end-pumping method)
Auto-focus function
KEYENCE'sMD-X2 Serieslaser markers have a built-in distance sensor that can autofocus to any location in the marking field without the need for external devices. As a result, it's able to maintain high marking quality on targets with variable size tolerances. Moreover, there's no need for downtime when a product type is changed, since the laser can be programmed to automatically accommodate. This greatly reduces labor-hours, simplifies facilities and improves productivity.
Measurement may not be possible depending on the material, shape, or surface condition of the target.
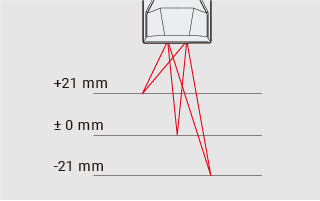
Marking patterns
KEYENCE laser markers provide several 2D code marking patterns that are optimized for different marking types. The following examples show how much difference a pattern change can make.
Selectable from various marking patterns
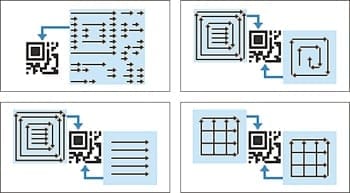
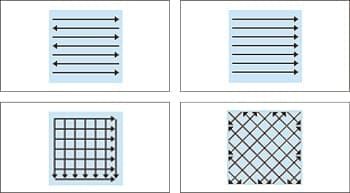
Clear 2D code marking
With some targets, reading may be unstable due to the influence of hairline metal surfaces. Just changing the marking pattern of a 2D code or base may improve the reading rate.
-
Target with hairline metal surface -
When the horizontal raster is used for the base processing, reading is unstable due to remaining hairlines. -
When the angled cross raster is used for the base processing, hairlines become invisible and reading is stable.
Fastest 2D code marking
Marking time may be limited depending on the desired production volume. Selecting an optimum marking pattern enables shorter marking time and improves productivity.
-
Pattern B Standard marking that marks cells one by one from left to right
Marking time: 637 ms
-
Entire pattern 2 高效的模式,标志着整个二维代码one stroke
Marking time: 342 ms
47% reduction from conventional method
The time was calculated with a marking example of 16 × 16 DataMatrix with cell size of 0.3 mm (0.01"). The evaluation above is a typical case. The result varies depending on the material and surface condition of the target and marking conditions.
2D code carving
Carving may be necessary in cases where parts are plated or hardened after being marked. Carving patterns enable a uniform amount of carving or engraving within a short time.
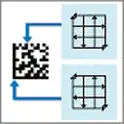
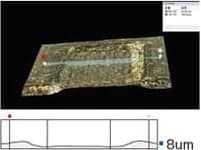
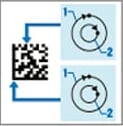
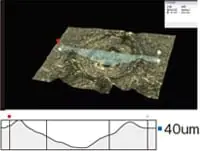